Simulación de moldeo por inyección basado en el método de volúmenes finitos (FVM)
DOI:
https://doi.org/10.17981/ingecuc.16.2.2020.08Palabras clave:
método de volúmenes finitos, moldeo por inyección, tiempos de enfriamiento, ciclo de vida del producto-PLM, diseño de experimentos, elementos finitosResumen
Introducción— Una de las principales preocupaciones en la industria de moldeo por inyección es garantizar un procesamiento eficiente de materiales y la adquisición de productos a costos razonables que reflejen sólidas economías de escalas para grandes series de producción. El tiempo de enfriamiento es una variable influyente y decisiva para la eficiencia de estas series, en ciertas condiciones de temperatura, aumenta junto con el espesor de la pieza. Por lo tanto, para cierto espesor, una baja temperatura del molde y una alta temperatura de extracción de la pieza tienen una influencia considerable en la reducción del tiempo de enfriamiento, lo que constituye un gran lapso del tiempo del ciclo de proceso: entre 80% y 85%. En este trabajo, el proceso de moldeo por inyección se simula para explorar la distribución de la temperatura y el proceso de llenado del material de un molde diseñado para hacer “etiquetas de oreja-chapetas”, que se utilizan para el control visual del ganado.
Objetivo— Como objetivo fundamental se busca identificar las variables esenciales en el proceso (tiempos de cierre y llenado del molde, presiones de inyección y empaquetamiento, fuerzas de sujeción y velocidad de inyección), así como su influencia en los tiempos de enfriamiento y la distribución de temperaturas finales del molde.
Metodología— Para lo anterior se establece una metodología de Diseño de Experimentos (DOE) basado en el diseño factorial 2k, partiendo de simulaciones basadas en el Método de Volúmenes Finitos (FVM).
Resultados— Este DOE, adaptado a los resultados numéricos, revela como resultado fundamental de este trabajo, las variables de estudio que son inherentes en el proceso, además de lograr su caracterización.
Conclusiones— Los resultados permitieron estudiar el comportamiento de la distribución de la temperatura en el molde, identificando como variables fundamentales a considerar en la experimentación: la temperatura inicial del molde y las interacciones comprendidas entre tiempo de enfriamiento - empaquetamiento y tiempo de enfriamiento-temperatura inicial del molde.
Descargas
Citas
M. E. Cendón Vásquez, Introducción al método de los volúmenes finitos. SCQ, ES: USC, 2008.
J. Gong, L. Xuan, B. Ying, & H. Wang, “Thermoelastic analysis of functionally graded porous materials with temperature-dependent properties by a staggered finite volume method,” Compos. Struct., vol. 224, no. 947, pp. e111071, Sep. 2019. https://doi.org/10.1016/j.compstruct.2019.111071
N. S. Myers & L. Kramer, “Simulation and experimental verification of two cavity balance in injection molding,” in Advances in Powder Metallurgy and Particulate Materials2019, NJ: MPIF, pp. 212–224 , 2020 .
G. R. Berger, D. Zorn, W. Friesenbichler, F. Bevc, & C. J. Bodor, “Efficient cooling of hot spots in injection molding. A biomimetic cooling channel versus a heat-conductive mold material and a heat conductive plastics,” Polym. Eng. Sci. , vol. 59, no. s2 , pp. E180–E188, 2019. https://doi.org/10.1002/pen.25024
R. Schiffers, M. Janßen, J. P. Siepmann, J. Wortberg, & F. A. Heinzler, “Using 3D injection molding simulation to explain emerging two- and three-dimensional surface structures of ABS and PC/ABS parts within the process of electroplating on plastics,” AIP Conf Proc, vol. 2065, pp. 30002-1–30002-5, 2019. https://doi.org/10.1063/1.5088260
S. Kumar & A. K. Singh, “Volumetric shrinkage estimation of benchmark parts developed by rapid tooling mold insert,” Sadhana - Acad. Proc. Eng. Sci., vol. 45, no. 1, pp. 1–9, May. 2020. https://doi.org/10.1007/s12046-020-01373-7
Moldex 3D, “¿Qué es Moldex 3D? - Moldex3D,” Moldex3d.es, [online . Available: http://www.moldex3d.es/moldex3d-software-simulacion-inyeccion-materiales-plasticos/que-es-moldex-3d/ [Accessed: 10-Aug-2020.
J. Pedro, B. Ramôa, J. M. Nóbrega, & C. Fernandes, “Verification and validation of openInjMoldSim, an open-source solver to model the filling stage of thermoplastic injection molding,” Fluids, vol. 5, no. 2, pp. 1–24, May. 2020. https://doi.org/10.3390/fluids5020084
Y. Niño, Metodo de volumenes finitos. (Sem. Primavera 2002). Modelacion numerica en ingenieria hidraulicay ambiental. CL: Uchile. Available: https://www.u-cursos.cl/ingenieria/2008/2/CI71D/1/material_docente/bajar?id=200975
J. Osses, “El método de volúmenes finitos,” Tecnología de Simulación, Fluidodinámica, 2016.
I. Sokolova, M. G. Bastisya, & H. Hajibeygi, “Multiscale finite volume method for finite-volume-based simulation of poroelasticity,” J. Comput. Phys., vol. 379, pp. 309–324, Feb. 2019. https://doi.org/10.1016/j.jcp.2018.11.039
M. Moayyedian, K. Abhary, & R. Marian, “Elliptical cross sectional shape of runner system in injection mold design,” Int. J. Plast. Technol., vol. 20, no. 2, pp. 249–264, Jul. 2016. https://doi.org/10.1007/s12588-016-9153-4
S. Kitayama and S. Natsume, “Multi-objective optimization of volume shrinkage and clamping force for plastic injection molding via sequential approximate optimization,” Simul. Model. Pract. Theory, vol. 48, pp. 35–44, Nov. 2014. https://doi.org/10.1016/j.simpat.2014.07.004
S. Hashimoto, S. Kitayama, M. Takano, Y. Kubo, & S. Aiba, “Simultaneous optimization of variable injection velocity profile and process parameters in plastic injection molding for minimizing weldline and cycle time,” J. Adv. Mech. Des. Syst. Manuf., vol. 14, no. 3, pp. JAMDSM0029, 2020. https://doi.org/10.1299/jamdsm.2020jamdsm0029
S. Hua, “Experimental and numerical investigation of jetting phenomenon in injection molding,” J. Brazilian Soc. Mech. Sci. Eng., vol. 42, no. 4, pp. 1–13, Mar. 2020. https://doi.org/10.1007/s40430-020-02278-6
T. Wöhner, A. Islam, H. N. Hansen, G. Tosello, & B. R. Whiteside, “Blister formation in film insert moulding,” Micromachines, vol. 11, no. 4, pp. 1–11, Apr. 2020. https://doi.org/10.3390/mi11040424
W. Z. Nie & T. P. Shi, “Prediction of plastic injection shrinkage ratio using grey theory,” Adv. Mater. Res., vol. 1028, pp. 96–104, Sep. 2014. https://doi.org/10.4028/www.scientific.net/AMR.1028.96
Q. Li, L. Li, X. Si, & W. Rongji, “Modeling the effect of injection molding process parameters on warpage using neural network theory,” J. Macromol. Sci. Part B Phys., vol. 54, no. 9, pp. 1066–1080, Sep. 2015. https://doi.org/10.1080/00222348.2015.1068680
J. H. Han & Y. C. Kim, “Study on Effects of Mold Temperature on the Injection Molded Article,” Arch. Metall. Mater., vol. 62, no. 2, pp. 1271–1274, 2017. https://doi.org/10.1515/amm-2017-0191
G. Zheng, W. Guo, Q. Wang, & X. Guo, “Influence of processing parameters on warpage according to the Taguchi experiment,” J. Mech. Sci. Technol., vol. 29, no. 10, pp. 4153–4158, Oct. 2015. https://doi.org/10.1007/s12206-015-0909-0
R. Surace, V. Bellantone, G. Trotta, & I. Fassi, “Replicating capability investigation of micro features in injection moulding process,” J. Manuf. Process., vol. 28, part. 1, pp. 351–361, Aug. 2017. https://doi.org/10.1016/j.jmapro.2017.07.004
Y. Chen & J. Zhu, “Warpage analysis and optimization of thin-walled injection molding parts based on numerical simulation and orthogonal experiment,” IOP Conf. Ser. Mater. Sci. Eng, vol. 688, no. 3, pp. 1–3, 2019. https://doi.org/10.1088/1757-899X/688/3/033027
C. M. Lin & W. C. Chen, “Optimization of injection-molding processing conditions for plastic double-convex Fresnel lens using grey-based Taguchi method,” Microsyst. Technol., vol. 26, no. 8, pp. 2575–2588, Mar. 2020. https://doi.org/10.1007/s00542-020-04798-6
Asteco, “Productos - Duraluminio 7075,” Asteco.com. Available: https://www.asteco.com.co/images/imagenes/productos/aceros/acerosparamoldes/fichastecnicas/7075.pdf
Petroquim, “PP Homopolímero PH1310_ Plassol,” Petroquim.cl, Dic. 2012. Available: http://www.petroquim.cl/wp-content/uploads/2012/12/FT-PH1310-Dic-2012.pdf
W. Pötsch, G., Michaeli, Injection Molding 2E. An Introduction. Ltpy. Twp, Oh., USA: Hanser Gardner Publications, 2007 .
S. Sánchez, I. G. Yáñez, & O. S. Rodríguez, Moldeo por inyección de termoplásticos. CDMX, MX: LIMUSA, 2005.
J. M. Almarrán, “Diseño y fabricación de un molde para inyección en Plástico,” Trabajo de grado, Dpto. Ing. Dis. Mec., ICAI, Md., Es., May. 2014.
F. L. Osswald Tim, Menges Georg, Flórez Jairo, Ciencia de los polímeros para ingenieros. Cuc., Co.: Editorial Guaduales Limitada, 2010.
D. C. Montgomery, Design and analysis of experiments. 5th ed., NY., USA: Hardcover, 2001.
C. Vargas, J. Sierra, J. Posada, & J. Botero, “Analysis and modeling of simulated residual stress of mold injected plastic parts by using robust correlations,” Rev. Mater., vol. 22, no. 4, pp. 1–13, Oct. 2017. https://doi.org/10.1590/s1517-707620170004.0228
A. ÖSTERGREN, “Prediction of residual stresses in injection moulded parts,” Master´s Thesis in the Applied Mechanics, Dpt. Appl. Mech., CUT, Gbg., Se., 2013. Available: https://publications.lib.chalmers.se/records/fulltext/179639/179639.pdf
J. A. P. de Oliveira, “Análise numérica de tensões induzidas pelo escoamento não isotérmico de um polímero no preenchimento de cavidades de paredes finas,” Grau de Doutor, dpto. eng. qui, UFRGS, RS, BR, 2012. Available: https://lume.ufrgs.br/handle/10183/75762
A. Nita & E. Oanta, “Improving the quality of the molded polymeric parts by reducing the residual stress,” 2nd International Conference on Manufacturing Engineering, Quality and Production Systems, MEQAOS10, Cnd., Ro., pp. 77–82, Sep. 3-5, 2010. Available: http://www.wseas.us/e-library/conferences/2010/Constantza/MEQAPS/MEQAPS-14.pdf
C. Vargas, J. Sierra, J. Posada, and J. Botero, “Analysis and modeling of simulated residual stress of mold injected plastic parts by using robust correlations,” Rev. Mater., vol. 22, no. 4, pp. 1–13, Oct. 02, 2017. https://doi.org/10.1590/s1517-707620170004.0228
A. Guevara-Morales and U. Figueroa-López, “Residual stresses in injection molded products,” J. Mater. Sci., vol. 49, no. 13, pp. 4399–4415, Mar. 2014. https://doi.org/10.1007/s10853-014-8170-y
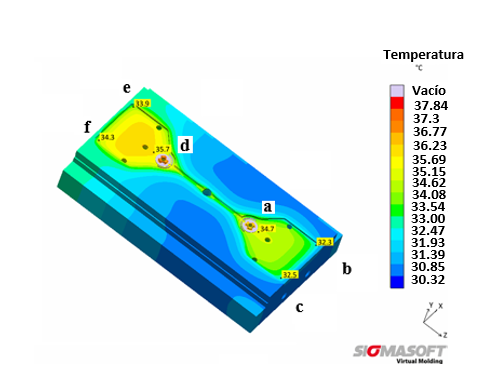
Publicado
Cómo citar
Número
Sección
Licencia
Derechos de autor 2020 INGE CUC

Esta obra está bajo una licencia internacional Creative Commons Atribución-NoComercial-SinDerivadas 4.0.
Los artículos publicados son de exclusiva responsabilidad de sus autores y no reflejan necesariamente las opiniones del comité editorial.
La Revista INGE CUC respeta los derechos morales de sus autores, los cuales ceden al comité editorial los derechos patrimoniales del material publicado. A su vez, los autores informan que el presente trabajo es inédito y no ha sido publicado anteriormente.
Todos los artículos están bajo una Licencia Creative Commons Atribución-NoComercial-SinDerivadas 4.0 Internacional.