Evaluation of surface hardness of NiCr coating using Finite Elements Analysis
DOI:
https://doi.org/10.17981/ingecuc.17.1.2021.24Keywords:
hardness test, finite elements, composite material, coating, simulationAbstract
Introduction: To enhance resistance to surface damage of materials due to mechanical actions, there have been created many procedures that allow its modification for different needs. This leads to researches conducted to determine the changes achieved in the properties due to said procedures. One method commonly applied is, for example, physical means of vapor deposition of thin films on a surface. In recent years, many rational and empirical models have been proposed for the study of said properties. One of these models is computational analysis, which allows determining a great number of properties while avoiding applying destructive tests, achieving to reduce experimental time spent and costs of manufacture of test tubes as well as the test itself.
In this research, the hardness of a surface coating of Nichrome (NiCr 80-20) was determined with an indentation test modeled in Ansys, based on the finite elements' method.
Objective: To design a computational model that allows determining the surface hardness of material with coating
Method: The realization of this project was made with the software for engineering analysis ANSYS, and the model was made based on the Vickers Indentation Test regulation given by the ASTM, which states that the test must be done with a pyramidal diamond indenter, applying forces greater than 1 kgf.
Results: By running the respective numerical analysis for both the substrate and the coating, a surface hardness of 197.5073 VH was obtained for NiCr coating and surface hardness of 160.5809 VH for the S235 Steel (hardness of the interface).
Conclusions: It was determined that the model proposed is correct seeing as the values obtained for the Vickers' Hardness is approximately the same as the experimental value with an error of 0.7501% for the coating layer and 0.2605% for the substrate. It was also concluded that it is possible to use this same procedure to obtain the surface hardness for different materials than those treated in this article by using this tool.
In this research the hardness of a surface coating of Nichrome (NiCr 80-20) was determined with an indentation test modeled in Ansys, based on the finite elements’ method [1].
Objective: To design a computational model that allows to determine the surface hardness of a material with coating
Method: The realization of this project was made with the software for engineering analysis ANSYS, and the model was made based on the Vickers Indentation Test regulation given by the ASTM [2], which states that the test must be done with a pyramidal diamond indenter, applying forces greater than 1 kgf.
Results: By running the respective numerical analysis for both the substratum and the coating, a surface hardness of 197.5073 VH was obtained for the S235 Steel (hardness of the interface) and a surface hardness of 160.5809 VH for the NiCr coating.
Conclusions: It was determined that the model proposed is correct seeing as the values obtained for the Vickers’ Hardness is approximately the same as the experimental value with an error or 0.7501% for the substratum and 0.2605% for the coating layer. It was also concluded that it is possible to use this same procedure to obtain the surface hardness for different materials than those treated in this article by using this tool.
Downloads
References
Eurocode.com, “Table of design material properties for structural steel,” eurocodeapplied.com, [online , 1993. Available: https://www.eurocodeapplied.com/design/en1993/steel-design-properties
N. F. Ak, C. Tekmen, I. Ozdemir, H. S. Soykan & E. Celik, “NiCr coatings on stainless steel by HVOF technique,” Surf Coat Technol, vol. 174-175, pp. 1070–1073, Sep. 2003. https://doi.org/10.1016/S0257-8972(03)00367-0
G. Faraji, H. S. Kim, & H. T. Kashi, “Chapter 7 - Mechanical Properties of Ultrafine-Grained and Nanostructured Metals,” in Severe Plastic Deformation, THR, IRN: Elsevier, pp. 223–257, 2018.
Z.-Q. Chen, H. Niu, D. Li & Y. Li, “Modeling hardness of polycrystalline materials and bulk metallic glasses,” Intermetallics, vol. 19, no. 9, pp. 1275–1281, Sep. 2011. https://doi.org/10.1016/j.intermet.2011.03.026
J. Gong, J. Wu & Z. Guan, “Examination of the indentation size effect in low-load vickers hardness testing of ceramics,” J Eur Ceram Soc, vol. 19, no. 15, pp. 2625–2631, Nov. 1999. https://doi.org/10.1016/S0955-2219(99)00043-6
J. M. Antunes, L. F. Menezes, & J. V. Fernande, “Three-dimensional numerical simulation of Vickers indentation tests,” Inter J Solids Struct, no. 43, pp. 784–806, 2006. https://doi.org/10.1016/j.ijsolstr.2005.02.048
A. Harish, “Finite Element Method – What Is It? FEM and FEA Explained”, simscale blog, Oct. 2020. Available: https://www.simscale.com/blog/2016/10/what-is-finite-element-method/
J. Zottis, C. A. T. Soares Diehl & A. da S. Roch, “Evaluation of experimentally observed asymmetric distributions of hardness, strain and residual stress in cold drawn bars by FEM-simulation,” J Mater Res Technol, vol. 7, no. 4, pp. 469–478, 2018. https://doi.org/10.1016/j.jmrt.2018.01.004
W. Han, K. Kuepper, P. Hou, W. Akram & H. Eickmeier, “Free-Sustaining Three-Dimensional S235 Steel-Based Porous Electrocatalyst for Highly Efficient and Durable Oxygen Evolution,” ChemSusChem, vol. 11, no. 20, pp. 3661–3671,Oct. 2018. https://doi.org/10.1002/cssc.201801351
H. Schäfer, K. Küpper, J. Wollshläger, N. Kashavae, J. Hardege, L. Walder, S. M. Beladi-Mousavi, B. Hartmann-Azanza, M. Steinhart, S. Sadaf & F. Dorn, “Oxidized Mild Steel S235: An Efficient Anode for Electrocatalytically Initiated Water Splitting,” ChemSusChem, vol. 8, no. 18, pp. 3099–3110, Sep. 2015. https://doi.org/10.1002/cssc.201500666
G. Marot, M. Martínez & J. Lesage, Modelado Computacional de un Ensayo Interfacial de Dos Materiales, 2007.
Designation E92-17: Standard Test Methods for Vickers Hardness and Knoop Hardness of Metallic Materials, ASTM E92, ASTM, 2017. https://doi.org/10.1520/E0092-17
D. R. Askenland, Ciencia e Ingeniería de los Materiales, 7 ed, BOS, USA: Cengage Learning, 2016.
A. Singh, K. Ramachandra & A. R. Devarhubli, “Evaluation and comparison of shear bond strength o porcelain to a beryllium-free alloy of nickel-chromium, nickel and beryllium free alloy of cobalt-chromium, and titanium: An in vitro study,” J Indian Prosthodont Socv, vol. 17, no. 3, pp. 261–266, 2017. https://doi.org/10.4103/jips.jips_337_16
SharcNet, “Ansys (Application),” sharcnet.ca, [online , 2016. Available: https://www.sharcnet.ca/my/software/show/22
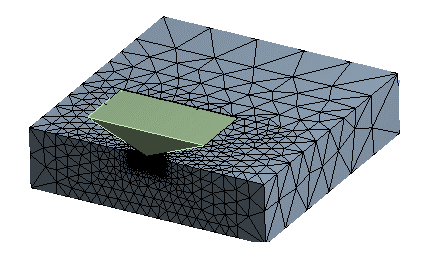
Published
How to Cite
Issue
Section
License
Copyright (c) 2021 INGE CUC

This work is licensed under a Creative Commons Attribution-NonCommercial-NoDerivatives 4.0 International License.
Published papers are the exclusive responsibility of their authors and do not necessary reflect the opinions of the editorial committee.
INGE CUC Journal respects the moral rights of its authors, whom must cede the editorial committee the patrimonial rights of the published material. In turn, the authors inform that the current work is unpublished and has not been previously published.
All articles are licensed under a Creative Commons Attribution-NonCommercial-NoDerivatives 4.0 International License.