Análisis CFD de flujos turbulentos desplazados por bombas centrífugas con bajo número de Reynolds
DOI:
https://doi.org/10.17981/ladee.01.01.2020.1Keywords:
CFD, Modelos de turbulencia, Estudio de independencia de malla, OpenFOAM, Bomba centrífugaAbstract
Numerical methodologies have presented an inexpensive solution of laminar and turbulent flows capable of predicting a wide range of mechanical devices in science and engineering. Computational tools have been employed in recent years to analyze the conservation equations behavior used to describe the interaction between turbulent and laminar flows used to transfer the energy needed to perform a complex mechanical system. Due to the above, this paper purpose the application of the numerical method linked to mathematical algorithms capable of generating an approximated solution of the partial differential equations system which determines pressure, and velocity values related to the centrifugal pump performance under low Re conditions in a virtual environment through OpenFOAM software, and Salome 8.3.0. An independence mesh analysis was computed to study the computational effort required to establish an approximated turbulence phenomena description performed by the centrifugal pump into the virtual environment supported by MRFSimpleFoam solver.
Downloads
References
T. Capurso, L. Bergamini, and M. Torresi, “Design and CFD performance analysis of a novel impeller for double suction centrifugal pumps,” Nucl. Eng. Des., vol. 341, no. 2019, pp. 155–166, 2019, doi: 10.1016/j.nucengdes.2018.11.002.
S. Emani, M. Ramasamy, and K. Z. K. Shaari, “Discrete phase-CFD simulations of asphaltenes particles deposition from crude oil in shell and tube heat exchangers,” Appl. Therm. Eng., vol. 149, pp. 105–118, Feb. 2019, doi: 10.1016/J.APPLTHERMALENG.2018.12.008.
M. Cagnoli, A. de la Calle, J. Pye, L. Savoldi, and R. Zanino, “A CFD-supported dynamic system-level model of a sodium-cooled billboard-type receiver for central tower CSP applications,” Sol. Energy, vol. 177, pp. 576–594, Jan. 2019, doi: 10.1016/J.SOLENER.2018.11.031.
X. Wang et al., “Study on the water seal formation process in advanced PWR pressurizer using CFD method,” Ann. Nucl. Energy, vol. 135, p. 106949, Jan. 2020, doi: 10.1016/J.ANUCENE.2019.106949.
O. M. Ilori, A. J. Jaworski, and X. Mao, “Experimental and numerical investigations of thermal characteristics of heat exchangers in oscillatory flow,” Appl. Therm. Eng., vol. 144, pp. 910–925, Nov. 2018, doi: 10.1016/J.APPLTHERMALENG.2018.07.073.
W. Qu, J. Xiong, S. Chen, and X. Cheng, “High-fidelity PIV measurement of cross flow in 5 × 5 rod bundle with mixing vane grids,” Nucl. Eng. Des., vol. 344, no. February, pp. 131–143, 2019, doi: 10.1016/j.nucengdes.2019.01.021.
T. Ziegenhein, D. Lucas, G. Besagni, and F. Inzoli, “Experimental study of the liquid velocity and turbulence in a large-scale air-water counter-current bubble column,” Exp. Therm. Fluid Sci., vol. 111, no. October 2019, p. 109955, 2020, doi: 10.1016/j.expthermflusci.2019.109955.
W. Lyu and O. el Moctar, “Numerical and experimental investigations of wave-induced second order hydrodynamic loads,” Ocean Eng., vol. 131, no. May 2016, pp. 197–212, 2017, doi: 10.1016/j.oceaneng.2016.11.047.
W. Yu-qin and D. Ze-wen, “Influence of blade number on flow-induced noise of centrifugal pump based on CFD/CA,” Vacuum, vol. 172, p. 109058, 2020, doi: https://doi.org/10.1016/j.vacuum.2019.109058.
N. Zhang, J. Jiang, B. Gao, and X. Liu, “DDES analysis of unsteady flow evolution and pressure pulsation at off-design condition of a centrifugal pump,” Renew. Energy, vol. 153, pp. 193–204, 2020, doi: https://doi.org/10.1016/j.renene.2020.02.015.
H. Yousefi, Y. Noorollahi, M. Tahani, R. Fahimi, and S. Saremian, “Numerical simulation for obtaining optimal impeller’s blade parameters of a centrifugal pump for high-viscosity fluid pumping,” Sustain. Energy Technol. Assessments, vol. 34, pp. 16–26, 2019, doi: https://doi.org/10.1016/j.seta.2019.04.011.
K. Wang, G. Luo, Y. Li, R. Xia, and H. Liu, “Multi-condition optimization and experimental verification of impeller for a marine centrifugal pump,” Int. J. Nav. Archit. Ocean Eng., vol. 12, pp. 71–84, 2020, doi: https://doi.org/10.1016/j.ijnaoe.2019.07.002.
Z. Ge, D. He, R. Huang, J. Zuo, and X. Luo, “Application of CFD-PBM coupling model for analysis of gas-liquid distribution characteristics in centrifugal pump,” J. Pet. Sci. Eng., p. 107518, 2020, doi: https://doi.org/10.1016/j.petrol.2020.107518.
S.-S. Deng, G.-D. Li, J.-F. Guan, X.-C. Chen, and L.-X. Liu, “Numerical study of cavitation in centrifugal pump conveying different liquid materials,” Results Phys., vol. 12, pp. 1834–1839, 2019, doi: https://doi.org/10.1016/j.rinp.2019.02.009.
E. Terzi, A. Cataldo, P. Lorusso, and R. Scattolini, “Modelling and predictive control of a recirculating cooling water system for an industrial plant,” J. Process Control, vol. 68, pp. 205–217, Aug. 2018, doi: 10.1016/J.JPROCONT.2018.04.009.
T. C. Roumpedakis et al., “Experimental Investigation and CFD Analysis of Heat Transfer in Single Phase Subcooler of a Small Scale Waste Heat Recovery ORC,” in Energy Procedia, 2017, vol. 129, pp. 487–494, doi: 10.1016/j.egypro.2017.09.166.
H. Quan, Y. Guo, R. Li, Q. Su, and Y. Chai, “Optimization design and experimental study of vortex pump based on orthogonal test,” Sci. Prog., no. 1, pp. 1–20, 2019, doi: 10.1177/0036850419881883.
Y. Gao, X. Fan, and R. Dang, “Numerical characterization of the effects of flow rate on pressure and velocity distribution of pump as turbine,” 2019.
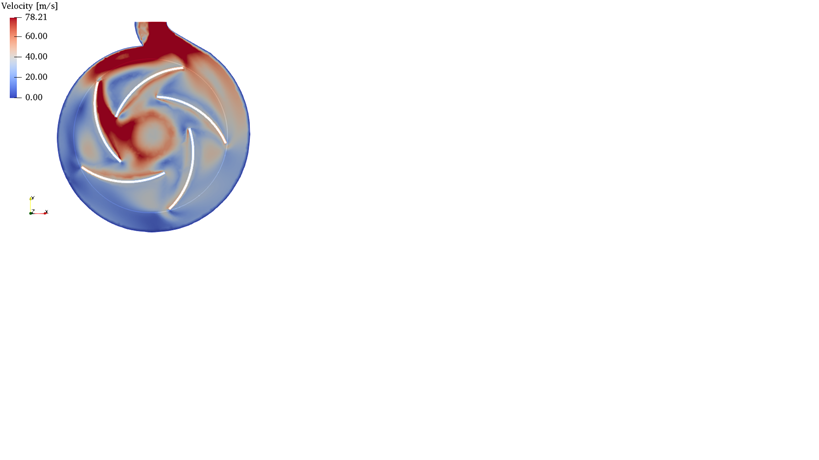
Downloads
Published
How to Cite
Issue
Section
License
You are free to:
- Share — copy and redistribute the material in any medium or format
- The licensor cannot revoke these freedoms as long as you follow the license terms.
Under the following terms:
- Attribution — You must give appropriate credit , provide a link to the license, and indicate if changes were made . You may do so in any reasonable manner, but not in any way that suggests the licensor endorses you or your use.
- NonCommercial — You may not use the material for commercial purposes .
- NoDerivatives — If you remix, transform, or build upon the material, you may not distribute the modified material.
- No additional restrictions — You may not apply legal terms or technological measures that legally restrict others from doing anything the license permits.